Bühler AG provides solutions for producing human food, animal feed, vehicle components and paints as well as for coatings on façades, eyewear and smartphones, and has been a valued partner of SFS since 2015. A family-run company, Bühler AG is headquartered in Uzwil (Switzerland) and has more than 12,700 employees in 140 countries. Innovations in new products, services and applications strengthen the market position of this global tech company, even in a difficult market environment.
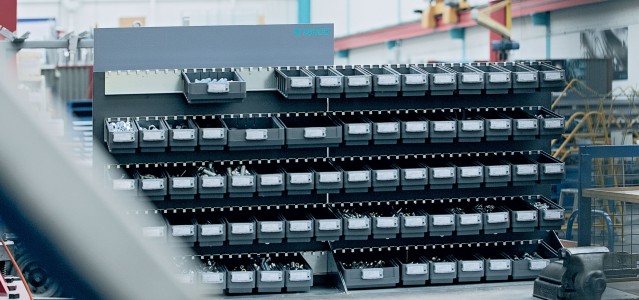
Proven partnership
as a success factor
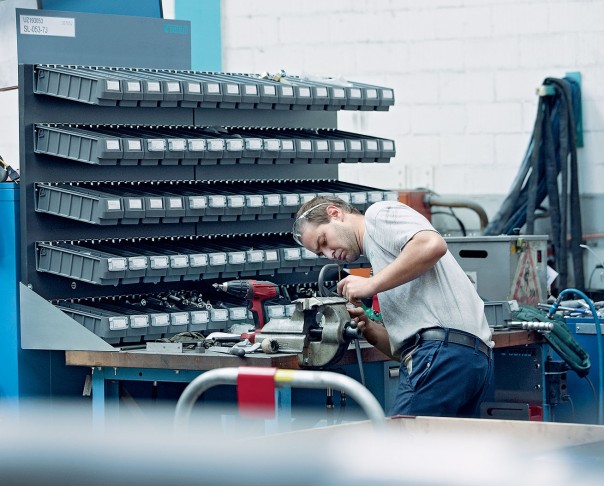
Proven system for C-part management
SFS furnishes Bühler with a wide range of fastening systems and tools, particularly in M2M systems like pushLOG®, which make it possible for Bühler to rely on a high level of local C-part availability. The system lets customers trigger an order at the press of a button and is particularly ideal for items that can be stored in containers. The new button with a large surface area makes operating the 2nd generation system even easier. Not only that, but pushLOG® 2 also offers the full range of functions for the new TAG, including delivery status updates or the integration of mobile devices. These systems have been supplied to several different Bühler plants since 2015, with more on the way.
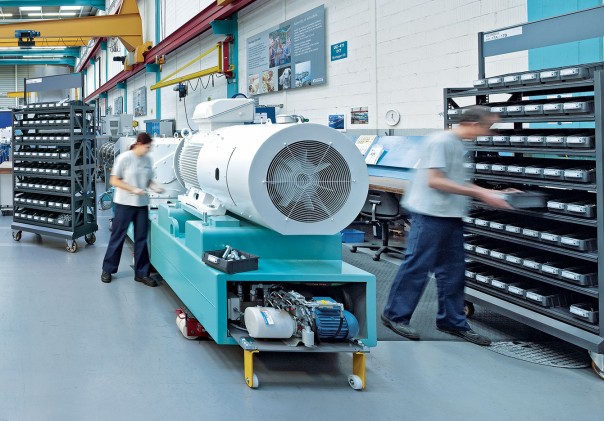
Strength through synergy
The constructive exchange of information, secure processes, and sparring sessions that form part of an ongoing improvement process all lay a solid foundation for our long-standing partnership. Our frank exchanges, reliability and collaboration based on trust helped us successfully navigate the supply bottlenecks and their repercussions on global supply chains. Together. And that makes us proud.
SFS uses a front-load warehouse, a type of distribution center, to cover the needs of Bühler’s facility in Uzwil and coordinates incoming and outgoing orders for the some 140 points of delivery inside the plant – fully electronically using the pushLOG® systems. SFS’s own Merchandising Team monitors and coordinates operations at the front-load warehouse to identify any shortages at an early stage.
Easy handling for greater flexibility
Fully automatic order placement at the push of a button, simple, self-explanatory operation, and the ability to check an order’s status at any given time make it easy for Bühler’s employees to become proficient with the process and boost flexibility.
We look forward to our ongoing partnership with Bühler!